Injection Molding
Shaping precision
for medical innovation
Injection molding is our core competence. We offer high-volume, cleanroom production using clamping forces from 150 to 3800 kN, supported by high-performance tooling from single to high cavitation. Our expertise in producing complex parts with the smallest tolerances enables efficient, scalable manufacturing for medical and pharmaceutical applications – all under ISO 13485 certified conditions.
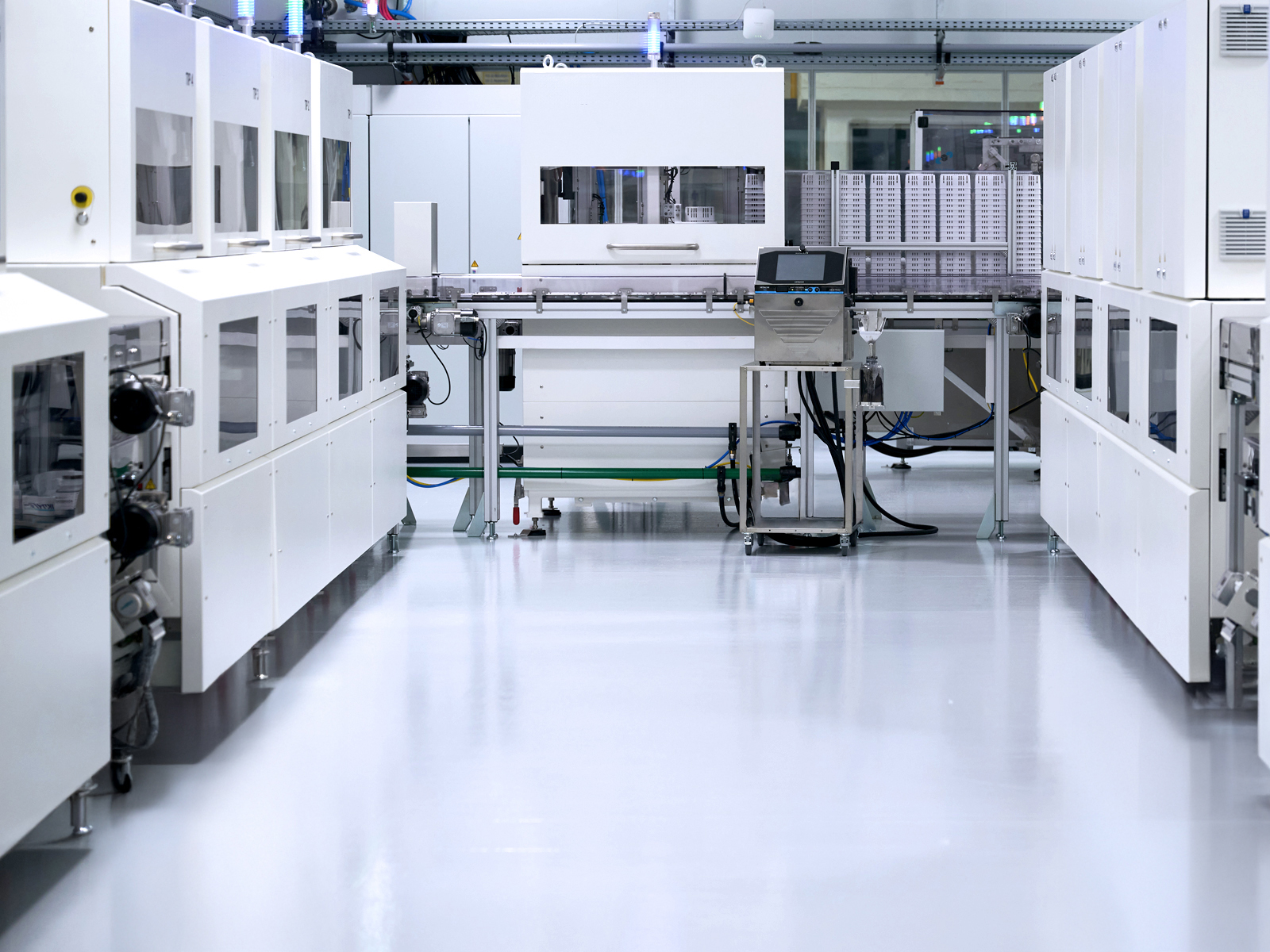
Cleanroom production
Our injection molding operations are conducted in ISO Class 7 and 8 cleanrooms, ensuring the highest standards of product quality, safety, and compliance. From material handling to final part production, every step is designed to meet the strict requirements of medical and pharmaceutical applications.
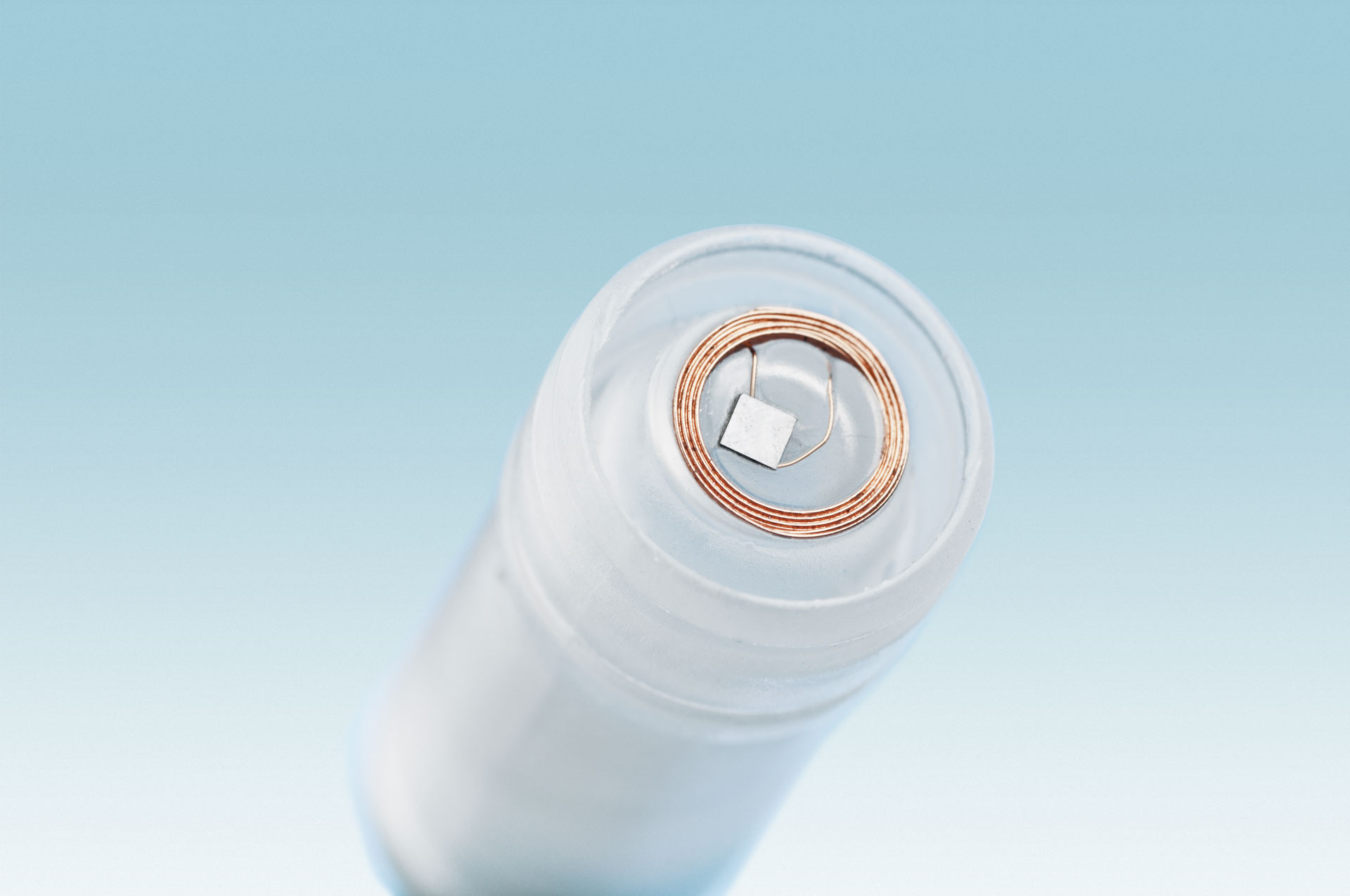
Insert molding
Insert molding allows us to integrate metal or plastics inserts into a single molded component with maximum precision. This technology improves product performance, reduces assembly steps, and is ideal for medical devices requiring robust and miniaturized solutions.
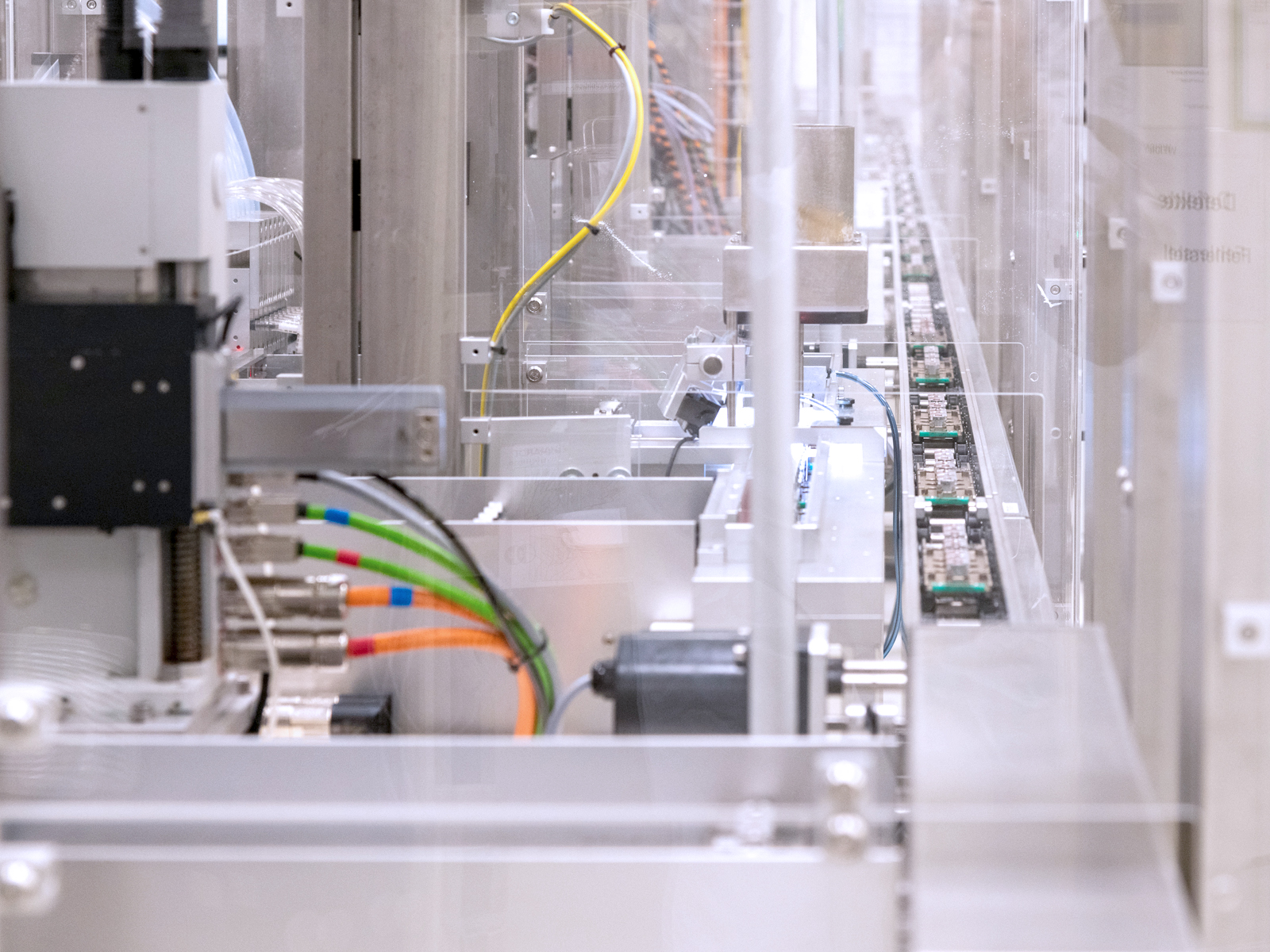
Multi-component molding
Our multi-component molding capabilities combine different plastics or materials into one part during a single process. This approach reduces weight, simplifies assembly, and enables complex functional integration for innovative medical applications.
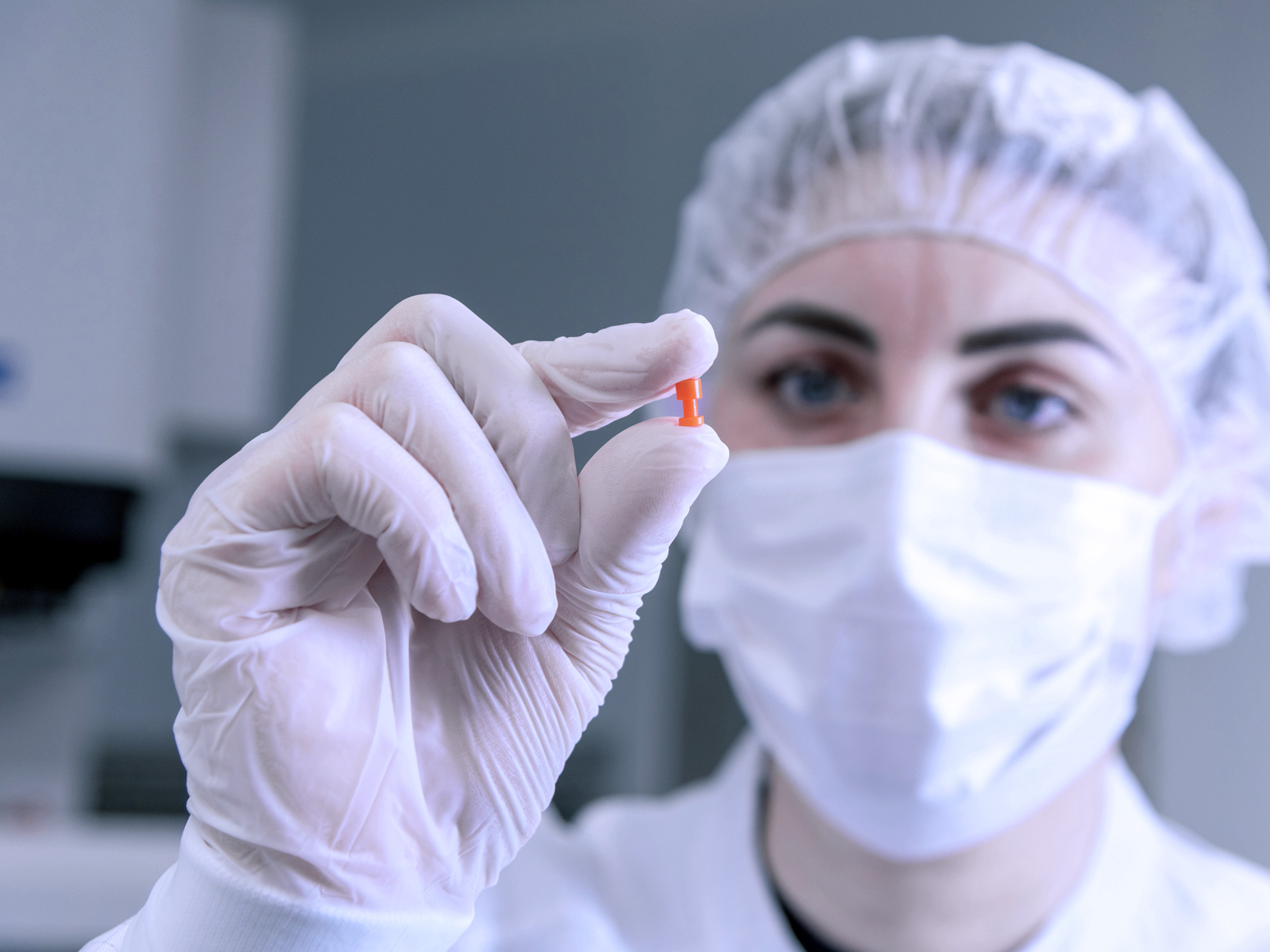
Micro molding
We specialize in micro injection molding for high-precision plastic parts with extremely small dimensions and tight tolerances. Using state-of-the-art micro injection molding machines, we ensure consistent quality and scalable cleanroom production for drug delivery and diagnostic components.
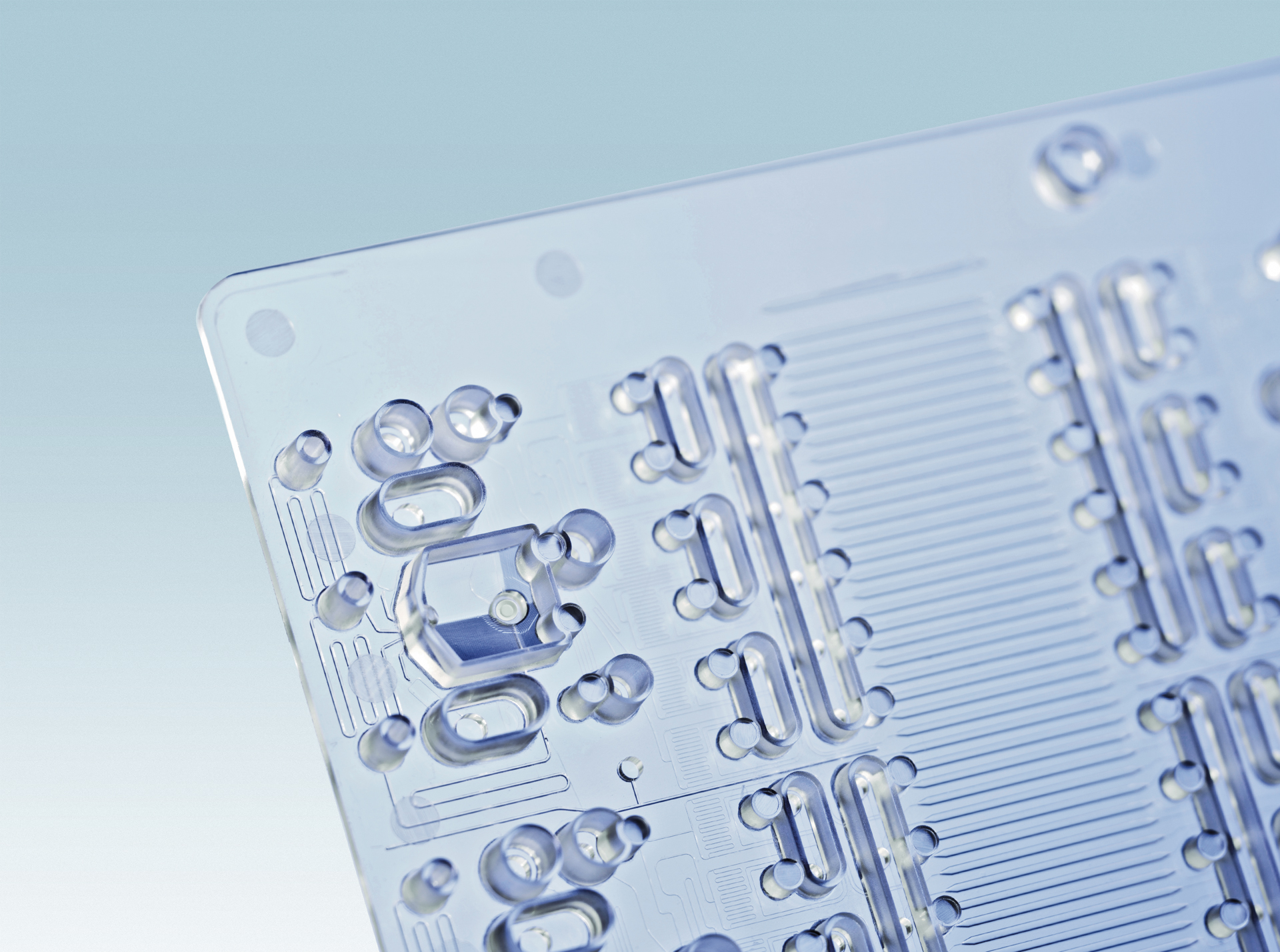
Microfluidics
We bring over 20 years of expertise in replicating micro- and nanostructures in plastics. We industrialize complex microfluidic components under cleanroom conditions with precise channel geometry, optimized part design, and reproducible manufacturing for high-volume diagnostic applications.
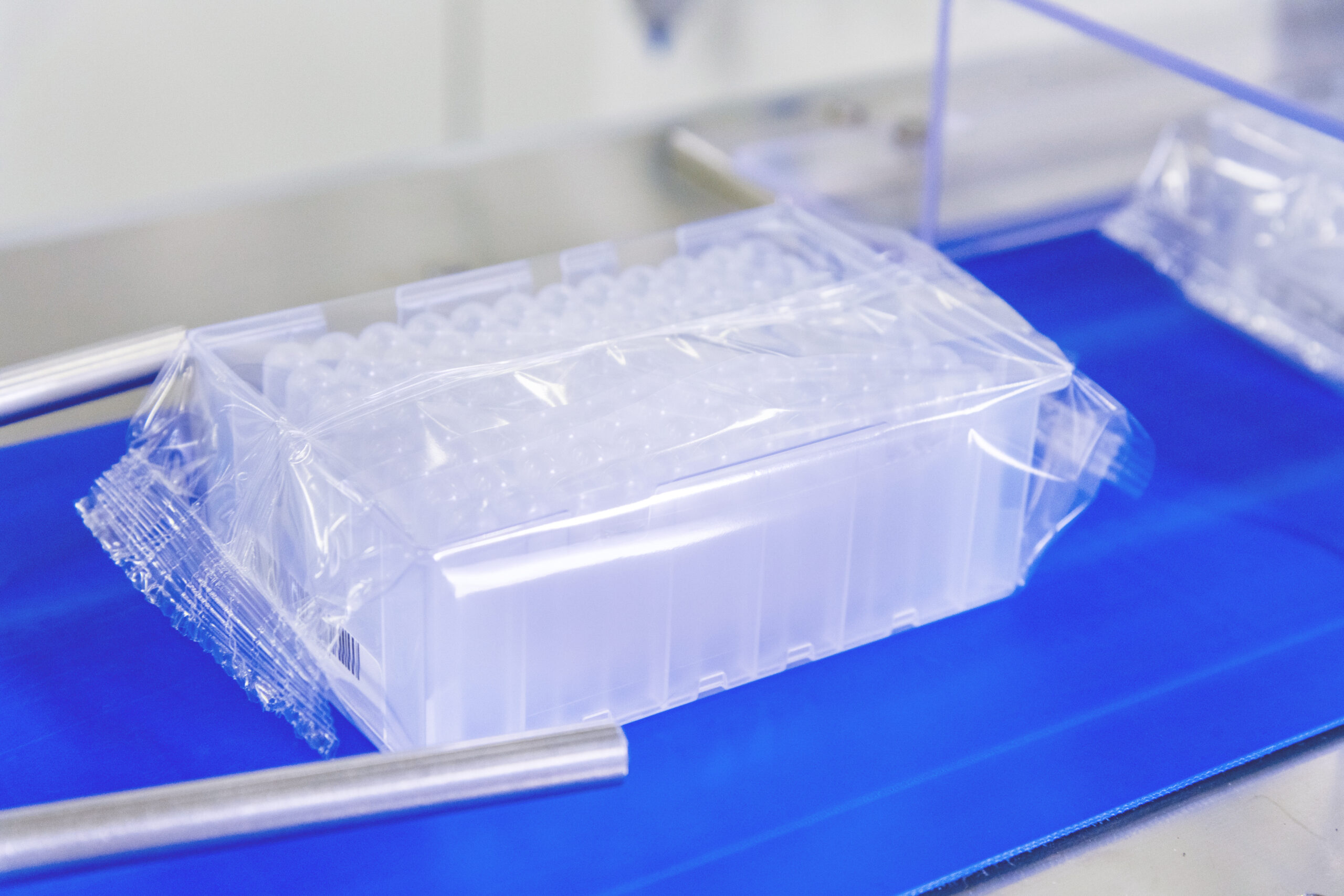
Post-processing technologies
We offer post-processing options such as in-mold labeling, laser marking, UV gluing, and cleanroom assembly to add value to your molded parts and ensure complete, ready-to-use solutions​.